Molding and Fabrication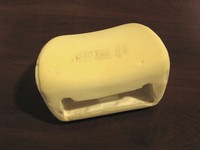 | An example of a molded foam part | Foam parts are usually formed by one of two methods. The first is molding. In this method, chemicals are mixed and injected into a mold, and allowed to solidify. When the part comes out of the mold it is ready for installation, no further fabrication steps are required. This process is ideal for the automotive industry where it is used to make seat cushions and other parts. This one step process results in a very low cost per part. The large production volumes associated with the manufacture of automobiles allow the relatively high cost of the tooling that is required to be spread over many units.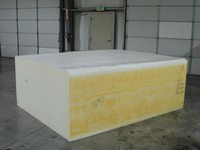 | A typical foam bun | The other method for creating foam parts is by fabricating them from large foam blocks called buns. In this process, the foam is first molded by injecting the chemicals into a large trough, or conveyer with tall sides. This produces a continuous block of foam that is cut off in sections or buns. A typical bun is approximately 108” x 82” x 30”, but buns can be almost any size and shape depending on the type of foam being produced, and the manufacturer. Once the buns are formed, they are usually cut or “slit” horizontally into sheets of whatever thickness is needed. These sheets are then cut into a variety of parts. For simple parts, this may be the last fabrication step, but usually several of these cutout parts need to be glued together to form the finished foam part that is ready for installation.Because of the additional steps involved, fabricated foam parts require more labor than molded parts. In addition they usually result in more material waste, and higher transportation costs. On the plus side though, they do allow for easy revisions of part design without costly retooling.
Continue >>
| Pages
[ << ]
[ 1 ]
[ 2 ]
[ 3 ]
[ 4 ]
[ 5 ]
[ 6 ]
[ >> ] |
|